As a customized training partner, WSU will assess and pinpoint your organization’s needs and develop specific training solutions to help your employees succeed and improve your bottom line. We deliver programming through the lens of a Continuous Quality Improvement Model which involves ongoing measurement and checkpoints to assure business goals are met.
The (Plan-Do-Check-Act) PDCA Cycle is the continuous improvement technique adopted by WSU. The four steps of the PDCA Cycle are:
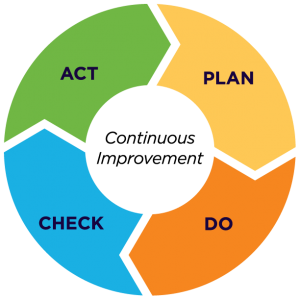
Source: ASQ, The Global Voice of Quality
- Plan:Identify an opportunity and plan for change.
- Do: Implement the change on a small scale.
- Check:Use data to analyze the results of the change and determine whether it made a difference.
- Act:If the change was successful, implement it on a wider scale and continuously assess your results. If the change did not work, begin the cycle again.
Even if your organization doesn’t actively promote a continuous quality improvement process today, that doesn’t mean you aren’t making progress. It just means that you’re probably not doing it as systematically or effectively as you could. This is where the notion of a culture of continuous quality improvement comes into play. When you explore using a continuous quality improvement process with your team, most will agree in the necessity but not necessarily know where to begin. Designing a formalized plan that works for your organization is critical.
Contact Julie Kiehne, WSU Business Outreach Coordinator, to discuss how the continuous quality improvement model can bring transformational change to your organization. jkiehne@winona.edu